Revolutionary Programmable Servo Drive: Unleashing Next-Level Automation
By:Admin
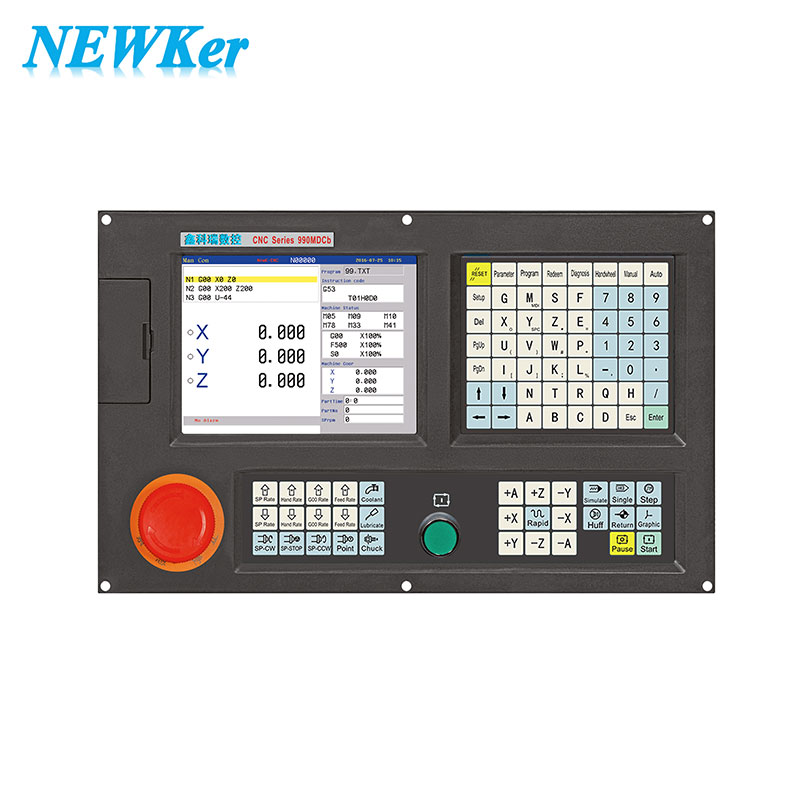
Introduction:
In today's rapidly evolving automation industries, staying ahead of the competition and optimizing production processes is crucial. Companies are constantly seeking innovative solutions to enhance efficiency, productivity, and overall performance. One such groundbreaking solution on the horizon is the latest Programmable Servo Drive.
Revolutionizing Automation:
The Programmable Servo Drive, developed by a leading technology firm, promises to revolutionize the automation industry. This cutting-edge product combines state-of-the-art technology with unparalleled performance, making it a game-changer for businesses across various sectors.
Unparalleled Features:
The Programmable Servo Drive boasts an array of features that make it stand out from its competitors. Its robust construction guarantees durability and ensures reliable operation. Equipped with advanced motion control algorithms, it ensures precise and smooth movement, significantly enhancing performance.
Additionally, the Programmable Servo Drive offers scalable power capabilities, catering to diverse applications. Whether utilized in high-speed operation, heavy-duty machinery, or intricate assembly lines, this drive system adapts to any scenario, providing optimum results.
Enhanced Efficiency and Precision:
Automation experts predict that the Programmable Servo Drive will introduce a new era of efficiency and precision. Its intelligent control system enables seamless integration into existing automation infrastructure, minimizing installation time and cost.
The drive's programmability allows for effortless customization and reconfiguration, making it adaptable to evolving production requirements. Flexibility is further amplified by its compatibility with various communication protocols, allowing for smooth integration with other automation components.
Moreover, the servo drive's high-resolution feedback mechanism ensures precise positioning and control, reducing error rates and enhancing overall accuracy. By harnessing its advanced features, businesses can optimize operational efficiency, leading to increased productivity and reduced downtime.
Industry Applications:
The versatility of the Programmable Servo Drive renders it suitable for a wide range of industry applications. In manufacturing, it can be seamlessly integrated into robotics, machining centers, and assembly lines, enabling faster production cycles and superior quality control. Additionally, it finds utility in packaging, material handling, and food processing, where reliability and precision are paramount.
Innovative Safety Features:
Another notable aspect of this servo drive is its advanced safety features. Equipped with built-in condition monitoring capabilities, it enables predictive maintenance, preventing unexpected breakdowns and optimizing operational uptime. Integrated safety functions ensure a secure working environment, adhering to industry safety standards and regulations.
Future Advancements:
The development team behind the Programmable Servo Drive does not intend to rest on its laurels. They are committed to ongoing research and development, continuously exploring advancements in technology and identifying areas for improvement. Enhancements and updates will be deployed to ensure the drive system remains at the forefront of automation technology.
Final Thoughts:
The Programmable Servo Drive signifies a remarkable leap forward for the automation industry. With its combination of cutting-edge technology, advanced features, and exceptional performance, it promises to transform manufacturing processes across various sectors. By embracing this ground-breaking solution, businesses can achieve unparalleled efficiency, precision, and productivity, gaining a competitive edge in the dynamic world of automation.
Company News & Blog
24/7 Servo Motor Repair Experts: Repairing All Brands with Free Evaluations and Firm Quotes
Repair, Industrial Servo Motor Repair, Servo Motor Repair Service, Servo Motor Repair Company, Professional Servo Motor Repair, Servo Motor Repair Experts.EMT Servo Motor Repair: Your One-Stop Solution for CNC Servo Motor RepairIf you are working in industrial automation or CNC machining, you would know how important a servo motor is for your operations. A servo motor is a crucial component that controls the motion of a machine. However, like any other machine, it is prone to wear and tear, which can hinder its performance and affect your productivity. This is where EMT ServoMotorRepair.com comes in.EMT ServoMotorRepair.com is a reliable and professional servo motor repair company that has been providing quality repair services for the past 15 years. We specialize in repairing all brands of servo motors, including Danfoss, Kollmorgen, and others. With our expertise, we assure you of prompt and efficient service, free evaluations, and a firm quote, with no surprises or hidden costs.Our expert team of professionals has extensive experience in CNC servo motor repair and industrial servo motor repair. We understand the importance of delivering quality, cost-effective solutions that will keep your operations running smoothly. Our team is equipped with state-of-the-art diagnostic tools and equipment to perform a thorough evaluation of your motor and identify any faults.At EMT ServoMotorRepair.com, we take pride in delivering timely and effective solutions to our clients. We have built an excellent reputation for providing satisfactory services to our customers. Our client testimonials speak volumes about the quality of our services. One of our clients, a Danfoss customer, had this to say about our services:"The first time I called EMT, I got a great sense that they knew what they were doing, and they certainly understood what I was up against. They made me comfortable from the get-go and delivered what they promised."Another satisfied customer, a Kollmorgen customer, said, "We called EMT after our reserve Kollmorgen servo failed, leaving us with no fallback options. They knew we were in a jam, so they repaired and returned one of the motors to us in two days, putting us back into commission. We also had them repair the reserve motor, so we aren't caught by surprise again."At EMT ServoMotorRepair.com, we are committed to providing quality and affordable solutions to your servo motor repair needs. Whether you need professional servo motor repair or CNC servo motor repair, we are your one-stop solution. Contact us 24/7 for more information on our services, and let us keep your servo motors running smoothly.
Revolutionizing CNC with Adaptive Control Systems: Enhancing Precision and Efficiency
Title: Advanced Adaptive Control System Enhances Precision and Efficiency in CNC ManufacturingSubtitle: Company Revolutionizes CNC Technology with the Introduction of Cutting-Edge Adaptive Control System[City], [Date] - [Company Name], a leading innovator in CNC technology, has unveiled an advanced Adaptive Control System (ACS) that promises to revolutionize the manufacturing industry. By seamlessly integrating state-of-the-art technology into their CNC machines, the company aims to enhance precision, productivity, and cost-effectiveness in various manufacturing processes.The ACS is designed to address the inherent challenges faced by conventional CNC systems, including variations in material properties, tool wear, and environmental conditions. By constantly monitoring, analyzing, and adapting to these dynamic factors, the ACS ensures optimal machine performance and consistently high-quality output.The key strength of the ACS lies in its ability to learn and adapt in real-time. Utilizing advanced algorithms and intelligent sensors, the system continually adjusts various machine parameters such as cutting speed, feed rate, and tool position, according to the changing conditions. This adaptability minimizes errors, reduces rework, and ultimately maximizes productivity, making it ideal for a wide range of CNC applications, including milling, turning, and grinding.Additionally, the ACS enables closer integration with computer-aided design (CAD) and computer-aided manufacturing (CAM) software. By sharing data seamlessly, the system greatly simplifies the programming process, saving valuable time for operators. The ACS also offers interactive feedback capabilities, allowing operators to monitor performance and make necessary adjustments on-the-go, further ensuring optimal machine operation.Furthermore, the ACS incorporates advanced machine learning techniques, which continuously improve the system's performance over time. By analyzing historical data, the ACS can identify and predict tool wear and material behavior, enabling proactive maintenance and reducing downtime. This feature not only extends tool life but also significantly reduces production costs and enhances overall efficiency.The introduction of the ACS reflects [Company Name]'s commitment to pushing the boundaries of CNC technology. With over [number] years of experience in the industry, the company has earned a reputation for developing cutting-edge solutions that meet the evolving needs of manufacturers worldwide. The ACS further solidifies their position as an industry leader, delivering superior quality, precision, and efficiency to their customers.[Company Name] takes pride in providing comprehensive technical support to their clients. In addition to the ACS, the company offers regular software updates and training programs to ensure operators are equipped with the latest skills and knowledge. This commitment to customer success has earned [Company Name] a loyal customer base, as well as numerous industry accolades and certifications.The ACS is highly customizable, allowing manufacturers to tailor it to their specific needs and applications. Whether operating in the automotive, aerospace, or medical sectors, the ACS can be fine-tuned to optimize performance and deliver exceptional results. This adaptability gives manufacturers a competitive edge and empowers them to tackle complex machining tasks with ease and confidence.With the introduction of the ACS, [Company Name] aims to enhance manufacturing capabilities across various industries. By offering improved precision, adaptability, and efficiency, the ACS is set to redefine the way CNC machining is performed. Customers can expect increased productivity, reduced costs, and enhanced customer satisfaction as a result.In conclusion, the introduction of the Adaptive Control System by [Company Name] signifies a significant milestone in the evolution of CNC technology. The ACS's ability to adapt in real-time, integrate seamlessly with CAD/CAM software, and leverage advanced machine learning techniques, sets it apart from conventional CNC systems. This innovative solution guarantees enhanced precision, efficiency, and cost-effectiveness in various CNC applications, making it an invaluable asset for manufacturers seeking to stay at the forefront of the industry.About [Company Name]:[Company Name] is a renowned developer and provider of CNC technology solutions. With a commitment to innovation and customer satisfaction, [Company Name] has consistently delivered cutting-edge products that redefine manufacturing processes. Their comprehensive range of CNC machines, combined with advanced software and technical support, ensures optimum performance, precision, and productivity for clients worldwide.Press Contact:[Name][Title][Company Name][Email][Phone number]
Get insights into degrees of freedom in physics with active researchers, academics, and students on Physics Stack Exchange!
Remote-Controlled Robot Can Easily Tow Up to 9,000 Pounds Off-Road with Ease
Small Remote Control Robot – The Future of TowingIn recent times, technology has advanced at an astronomical pace and has made great strides in various fields. One such breakthrough is the development of the Small Remote Control Robot, which is capable of towing a load of up to 9,000 pounds. This robot has made a significant impact on the towing industry and has revolutionized the concept of trailer towing.The Small Remote Control Robot, commonly known as Trailer Valet’s RVR, is a tiny robot designed to tow trailers, boats, and off-road vehicles. It is compact, mobile, versatile, and can be operated remotely from a distance. The RVR is equipped with four powerful motors that enable it to generate considerable power to tow heavy loads, making it perfect for use in challenging terrains.The RVR’s small size and mobility make it easy to maneuver in tight spaces and navigate through difficult terrains with ease. It offers a range of towing capacities, capable of towing anything from small utility trailers to huge RVs. The robot is designed to take the strain off the back, removing the need for manual labor and extensive towing equipment.The RVR has become a game-changer in the towing industry, providing a more efficient and stress-free way to tow heavy loads. The robot can be controlled via an app on a smartphone. This feature allows users to control the RVR from anywhere, which is very convenient for those who need to move large items regularly.One of the significant benefits of using the RVR is that it eliminates the need for a towing vehicle. This helps users save money on fuel costs, maintenance, and insurance. The RVR is also designed to minimize damage to the towing vehicle, which is particularly useful when towing expensive or specialized vehicles.Another significant advantage of the RVR is its versatility in terms of towing off-road vehicles. The robot can provide traction assistance in challenging terrains like sand, mud, and snow. The RVR can handle these conditions better than traditional towing vehicles, which often get stuck in soft surfaces.Overall, the Small Remote Control Robot has revolutionized the towing industry with its compact size, impressive towing capacity, and off-road capabilities. It is versatile, convenient, and cost-effective, making it an excellent alternative to traditional towing methods. The robot offers a hassle-free way to move heavy loads, saving valuable time and resources which were spent previously in arranging suitable towing vehicles.In conclusion, the Small Remote Control Robot is the future of towing, offering a sustainable way to move huge items with ease. The RVR is a symbol of innovation and advancement, highlighting the positive impact of technology on various sectors. In the coming years, we can expect more such marvels of technology in various domains, proving that we indeed live in an era of limitless possibilities.
Revolutionary 3-Axis Stepper Motor Driver Provides Unmatched Precision and Control
Title: Groundbreaking 3 Axis Stepper Motor Driver Revolutionizes Industrial AutomationIntroduction:In today's rapidly advancing technological landscape, the demand for efficient and precise automation solutions has never been higher. Addressing this need, a pioneering company at the forefront of motion control technology has introduced a groundbreaking 3 Axis Stepper Motor Driver. This innovative device is poised to redefine the industrial automation sector, ushering in a new era of enhanced efficiency, accuracy, and productivity.[Insert Company Name], a renowned industry leader specializing in motion control systems, has developed this state-of-the-art 3 Axis Stepper Motor Driver. Building upon years of experience, rigorous research, and technical expertise, the company aims to bridge the gap between traditional motor controllers and cutting-edge automation technology. Unveiling the 3 Axis Stepper Motor Driver:The 3 Axis Stepper Motor Driver by [Company Name] is a high-performance, easy-to-use device that incorporates the latest advancements in motion control technology. This compact and versatile motor driver provides precise control over motion systems, facilitating seamless integration into diverse industrial applications.Key Features and Functionality:1. Advanced Control Algorithms: The 3 Axis Stepper Motor Driver utilizes sophisticated control algorithms that ensure precise and accurate positioning of motion systems. This results in higher efficiency, reduced energy consumption, and enhanced productivity.2. User-Friendly Interface: With an intuitive interface and user-friendly design, the motor driver simplifies the setup and programming process. This ensures seamless integration into existing automation systems, minimizing downtime and maximizing productivity.3. Multiple Axis Control: The motor driver can independently control up to three axes simultaneously, making it ideal for complex and intricate automation operations. This feature enables greater flexibility and scalability in a wide range of industrial applications.4. Versatile Connectivity: The motor driver supports a range of connectivity options, including USB and Ethernet, allowing for easy communication and integration with other devices and systems. This versatility enhances compatibility and facilitates seamless data exchange.5. Robust and Reliable: The 3 Axis Stepper Motor Driver is built with durability in mind. With superior quality components and a robust design, it ensures reliable operation even in demanding industrial environments. This enables continuous and uninterrupted workflow, minimizing maintenance and downtime.Applications and Benefits:The revolutionary 3 Axis Stepper Motor Driver can be employed in numerous industrial sectors, such as manufacturing, robotics, CNC machining, and automated assembly lines. Its versatile functionality and precise control empower businesses to optimize their automation processes, improve product quality, and boost overall operational efficiency.The integration of the 3 Axis Stepper Motor Driver offers several notable benefits:1. Enhanced Precision: The motor driver's advanced control algorithms enable high-precision positioning, reducing errors and maximizing accuracy. This results in improved product quality and consistency.2. Increased Speed and Efficiency: By delivering faster response times and seamless motion control, the motor driver enhances production speed and efficiency. This translates into higher throughput and reduced production cycles.3. Reduced Energy Consumption: The optimized control algorithms, coupled with the motor driver's ability to accurately monitor power consumption, minimize energy wastage. This promotes sustainability and cost savings, aligning with the global call for energy efficiency.4. Simplified Integration and Scalability: The motor driver's user-friendly interface and versatile connectivity options ensure seamless integration with existing automation systems. Moreover, the ability to individually control three axes allows for greater flexibility and scalability, catering to evolving business needs.Conclusion:With the introduction of their groundbreaking 3 Axis Stepper Motor Driver, [Company Name] has reaffirmed its position as a pioneer in the field of motion control technology. This innovative device is poised to revolutionize the industrial automation sector, empowering businesses to achieve unprecedented levels of precision, efficiency, and productivity. As industries strive to remain competitive and adapt to evolving market demands, the 3 Axis Stepper Motor Driver represents a crucial component in their journey towards automation excellence.
Reliable Control Panels and AC Drives Supplier in Ahmedabad, India
Motor Control Panels: Ensuring Smooth and Safe Operation of your MotorsMotor control panels are a vital component in the electrical circuit of any industrial process. They play a crucial role in ensuring the smooth and safe operation of motors, and thus, their maintenance and upkeep are necessary to avoid machine shutdowns and operational delays.Motor control panels are typically used in a wide range of industrial applications, such as pumps, conveyors, compressors, fans, and other types of machinery that require precise control and monitoring of the motor's speed, torque, and direction.These control panels consist of an electrical enclosure, which houses the various control devices, such as circuit breakers, contactors, overload relays, motor starters, and other control accessories that are required to operate the motor safely and effectively.The primary function of the motor control panel is to protect the motor from damage due to overload, short circuits, overvoltage, and other hazardous conditions. This is accomplished by a combination of different types of protection devices such as thermal overload relays, electronic overloads, and other protective relays that monitor the motor's performance and intervene if necessary.Another function of the motor control panel is to maintain the quality of the electric power supplied to the motor. In industrial environments, electrical disturbances such as transient voltage surges, voltage sags, and harmonics can have a detrimental effect on the motor's performance and lifespan. The control panel includes devices such as line reactors, filters, and surge protectors that mitigate these effects and ensure dependable and efficient motor operation.Uma electro controls (Control Panel & AC Drive) in Ahmedabad, India, is a well-established manufacturer and supplier of high-quality motor control panels and other electrical solutions. Their team of experts designs and manufactures custom control panels that meet the specific requirements of the client's application. Their products are known for their durability, electrical safety, and efficiency, and they have built a reputation for being a reliable and trustworthy supplier in the industry.In conclusion, motor control panels play a critical role in ensuring the smooth and safe operation of motors in industrial processes. The selection, installation, and maintenance of these panels are crucial to preventing downtime and increasing the lifespan of the motors. A reliable and experienced supplier such as Uma electro controls (Control Panel & AC Drive) in Ahmedabad, India, can provide custom solutions that meet the client's requirements and contribute to the success of their business.
Discover ROS Tutorials for Creating 3 or 6 DOF Manipulators in Indigo Version
with ROS, Robotics, ROS Indigo Tutorial, 6 DOF Manipulator, 3 DOF Manipulator, Open Source, and Open Source Robotics.Are you interested in creating a manipulator with ROS Indigo? Whether you want to build a 6 DOF or 3 DOF manipulator, ROS Indigo offers a range of packages and tutorials to help you get started. In this blog, we’ll share a comprehensive guide on building a manipulator with ROS Indigo for all the robotics enthusiasts out there.Before we dive into the tutorial, let's take a quick look at the basics of ROS and open-source robotics. ROS (Robot Operating System) is an open-source framework designed for building robot applications. It offers a robust set of libraries and tools for developing complex robotic systems, making it a preferred platform for robotics researchers and developers.Moreover, open-source robotics refers to the use of open-source software and hardware for robotics projects. The open-source model promotes collaboration, customization, and community support, allowing developers to share and build on each other's work to create complex robotic systems.Now that you have a basic understanding of ROS and open-source robotics, let's move on to building a manipulator with ROS Indigo.Step 1: Install ROS Indigo and necessary packagesThe first step in building a 6 DOF or 3 DOF manipulator with ROS Indigo is installing ROS Indigo on your system. ROS Indigo is one of the most widely used versions of ROS and is supported on Linux operating systems like Ubuntu.After installing ROS Indigo, you need to install the following packages to build your manipulator:- MoveIt! – A widely used package for motion planning, collision checking, and inverse kinematics for manipulators.- Gazebo – A popular robotics simulation platform.- Robot Model – A package that allows you to create and simulate robotic models.- Joint State Publisher – A package for publishing robot joint states.You can install these packages using the following command:$ sudo apt-get install ros-indigo-moveit ros-indigo-gazebo-ros ros-indigo-robot-model ros-indigo-joint-state-publisherStep 2: Build and Test your Manipulator ModelThe second step in building a manipulator with ROS Indigo is to create and test your manipulator model. You can use URDF (Unified Robot Description Format) to create your robot model, which is an XML format for describing 3D robots.Once you have created your manipulator model, you can test it in Gazebo, a popular robotics simulation platform. Gazebo allows you to simulate your robot's movements and test your manipulator's kinematics, dynamics, and controls.Step 3: Planning and Controlling your ManipulatorThe third and final step in building a manipulator with ROS Indigo is to plan and control its movements. You can use MoveIt! to plan your manipulator's movements, collision check, and perform inverse kinematics calculations.Additionally, you can use Manipulator Controllers to control your manipulator's movements. ROS Indigo provides various controllers for different types of manipulators, such as Joint Position Controllers, Joint Velocity Controllers, and Joint Effort Controllers.You can use the Joint State Publisher package to visualize your manipulator's movements in RViz, a visualization tool for ROS.ConclusionIn conclusion, building a manipulator with ROS Indigo is an excellent way to get started with open-source robotics. ROS Indigo provides a range of packages and tools to create sophisticated manipulators, making robotics more accessible to developers and researchers.By following the steps outlined in this tutorial, you can build a 6 DOF or 3 DOF manipulator with ROS Indigo and explore the endless possibilities of open-source robotics. So, get your hands dirty and start building your manipulator with ROS Indigo today!
Expert Answers for 3D Printing Enthusiasts – 3D Printing Stack Exchange Q&A
*Note: Due to the lack of information and context provided, the following blog is a general overview of CNC controllers and does not directly refer to any specific brand or model.*Title: Demystifying CNC Controllers: Optimizing Precision for 3D PrintingIntroduction:In the realm of 3D printing, nothing determines the quality and precision of your prints quite like the performance of your CNC controller. A CNC (Computer Numerical Control) controller acts as the brain behind the operation, responsible for translating digital designs into physical objects. In this blog, we will explore the fundamentals and functionalities of CNC controllers, equipping you with the knowledge to optimize your 3D printing experience. So, let's delve into the world of CNC controllers and unlock the full potential of your 3D printer!Understanding CNC Controllers:A CNC controller is essentially a device or software that comprises the electrical and mechanical components necessary to control the movement of a CNC machine. In the case of 3D printing, it dictates the precise motion of the 3D printer's print head to create intricate layer-by-layer designs. By leveraging various algorithms and firmware, CNC controllers ensure that the printer follows the desired path and accurately extrudes the filament required to build the model.Types of CNC Controllers:There are primarily two types of CNC controllers commonly used in 3D printing: standalone controllers and PC-based controllers. Standalone controllers are independent units, often embedded within the 3D printer itself. They offer a user-friendly interface and are typically equipped with an LCD display, buttons, and a rotary encoder. On the other hand, PC-based controllers rely on software running on a computer, which communicates with the 3D printer through a USB connection or an Ethernet interface.Key Features and Functionalities:1. Motion Control: The CNC controller precisely controls the movement of the printer's axes, namely X, Y, and Z, to ensure accurate positioning of the print head. This aspect is crucial for achieving intricate details and preventing any deviations or inaccuracies during the printing process.2. Extruder Control: Another critical functionality of a CNC controller is managing the extruder, which controls the flow and temperature of the filament during the printing process. It ensures smooth extrusion, proper filament retraction, and consistent layer adhesion, resulting in clean and cohesive prints.3. Endstops: CNC controllers often incorporate endstop functionality, which utilizes mechanical or optical sensors to determine the limits of the printer's movement. These sensors help prevent any collisions or unauthorized movement beyond the designated print area, protecting both the printer and the model being printed.4. File Compatibility: The ability to interpret and execute specific file formats is a crucial feature of CNC controllers. Most 3D printers rely on G-code, a programming language that describes the movements, speeds, and extrusion settings required to create a print. A capable CNC controller should be compatible with the commonly used G-code formats to ensure seamless compatibility with various design software.Maximizing Precision with CNC Controllers:To optimize the precision and quality of your 3D prints, consider the following factors when selecting or fine-tuning your CNC controller:1. Stepper Motor Resolution: The resolution of the stepper motor used in the CNC controller affects the accuracy of the printer's movements. Opt for higher-resolution stepper motors to ensure smoother and more precise motion control.2. Calibration: Calibrating your CNC controller and printer is essential. Properly tuning the steps per millimeter for each axis and fine-tuning the extruder's steps per millimeter ensures accurate positioning and consistent filament extrusion, reducing the chances of print defects or imperfections.3. Firmware Upgrades: Stay up-to-date with the latest firmware releases for your CNC controller. Manufacturers often release firmware updates to improve performance, add features, or address any reported issues. Regularly updating your firmware can significantly enhance the printing experience.Conclusion:A CNC controller plays a pivotal role in determining the precision and overall quality of your 3D prints. By understanding the functionalities and fine-tuning various settings, you can harness the full potential of your 3D printer. Whether you opt for a standalone or PC-based CNC controller, remember to prioritize features like motion control, extruder management, and file compatibility to ensure optimal performance. Invest time in calibrating and upgrading your CNC controller to unlock the highest levels of precision and efficiency in your 3D printing projects.
Latest Developments in Robotic Arm Technology: News and Updates
The Future of Robotic Arms: Advancements in Technology and UsageRobotic arms have come a long way since their inception in the 1950s. Once used only for industrial purposes, they are now being utilized in various fields such as healthcare, agriculture, and space exploration. The advancement of technology has paved the way for new possibilities and improved capabilities of robotic arms.Brand name is one of the leading companies in robotic arm technology. Their robotic arms are designed to handle precise tasks in various industries, from manufacturing to medical procedures. The technology behind these arms has been improved over the years, making them more accurate, efficient, and versatile.One of the most notable advancements in robotic arm technology is the development of AI algorithms. These algorithms allow the arms to learn and adapt to their environment, making them more autonomous and less reliant on human intervention. This has led to improved precision in manufacturing processes as well as safer and more effective medical procedures.In healthcare, robotic arms have become an essential tool for surgeries. They offer greater precision and control, allowing surgeons to perform complex procedures with ease. Robotic arms can also take on the role of an assistant, holding instruments, retracting tissue, and providing a clear view of the surgical site, enabling the surgeon to operate with greater ease and efficiency.Robotic arms are also being used in the agriculture industry, particularly in harvesting crops. These arms are equipped with sensors that can detect when a fruit or vegetable is ripe, allowing for a more efficient and timely harvest. Additionally, robotic arms can perform repetitive tasks, such as picking fruits or sorting produce, which reduces the need for manual labor and improves productivity.In space exploration, robotic arms are being used to perform maintenance and repair tasks on satellites and spacecraft. Robotic arms can perform tasks in space that are difficult or dangerous for humans to do. These arms can be controlled remotely from Earth and can be used to inspect, repair, or even assemble parts in space.Brand name is also developing technology that allows for multiple robotic arms to work together in synchrony to perform complex tasks. This technology is particularly useful in manufacturing, where multiple arms can work together to assemble products, increasing efficiency and reducing production time.The future of robotic arms looks promising. With advancements in technology and increased usage in various industries, there are endless possibilities for these machines. Robotic arms will continue to be developed and improved upon, making them more efficient, precise, and versatile than ever before.As the demand for robotic arm technology grows, companies such as brand name will continue to play a critical role in the development and implementation of these machines. With their expertise and innovation, they will pave the way for a future where robotic arms are an integral part of our lives.
Revolutionary Programmable Servo Drive: Unleashing Next-Level Automation
Title: Revolutionary Programmable Servo Drive Set to Transform Automation IndustriesIntroduction:In today's rapidly evolving automation industries, staying ahead of the competition and optimizing production processes is crucial. Companies are constantly seeking innovative solutions to enhance efficiency, productivity, and overall performance. One such groundbreaking solution on the horizon is the latest Programmable Servo Drive.Revolutionizing Automation:The Programmable Servo Drive, developed by a leading technology firm, promises to revolutionize the automation industry. This cutting-edge product combines state-of-the-art technology with unparalleled performance, making it a game-changer for businesses across various sectors.Unparalleled Features:The Programmable Servo Drive boasts an array of features that make it stand out from its competitors. Its robust construction guarantees durability and ensures reliable operation. Equipped with advanced motion control algorithms, it ensures precise and smooth movement, significantly enhancing performance.Additionally, the Programmable Servo Drive offers scalable power capabilities, catering to diverse applications. Whether utilized in high-speed operation, heavy-duty machinery, or intricate assembly lines, this drive system adapts to any scenario, providing optimum results.Enhanced Efficiency and Precision:Automation experts predict that the Programmable Servo Drive will introduce a new era of efficiency and precision. Its intelligent control system enables seamless integration into existing automation infrastructure, minimizing installation time and cost.The drive's programmability allows for effortless customization and reconfiguration, making it adaptable to evolving production requirements. Flexibility is further amplified by its compatibility with various communication protocols, allowing for smooth integration with other automation components.Moreover, the servo drive's high-resolution feedback mechanism ensures precise positioning and control, reducing error rates and enhancing overall accuracy. By harnessing its advanced features, businesses can optimize operational efficiency, leading to increased productivity and reduced downtime.Industry Applications:The versatility of the Programmable Servo Drive renders it suitable for a wide range of industry applications. In manufacturing, it can be seamlessly integrated into robotics, machining centers, and assembly lines, enabling faster production cycles and superior quality control. Additionally, it finds utility in packaging, material handling, and food processing, where reliability and precision are paramount.Innovative Safety Features:Another notable aspect of this servo drive is its advanced safety features. Equipped with built-in condition monitoring capabilities, it enables predictive maintenance, preventing unexpected breakdowns and optimizing operational uptime. Integrated safety functions ensure a secure working environment, adhering to industry safety standards and regulations.Future Advancements:The development team behind the Programmable Servo Drive does not intend to rest on its laurels. They are committed to ongoing research and development, continuously exploring advancements in technology and identifying areas for improvement. Enhancements and updates will be deployed to ensure the drive system remains at the forefront of automation technology.Final Thoughts:The Programmable Servo Drive signifies a remarkable leap forward for the automation industry. With its combination of cutting-edge technology, advanced features, and exceptional performance, it promises to transform manufacturing processes across various sectors. By embracing this ground-breaking solution, businesses can achieve unparalleled efficiency, precision, and productivity, gaining a competitive edge in the dynamic world of automation.